SeaBioComp Newsletter No2 May 2020
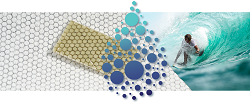
Welcome to the SeaBioComp Project Newsletter No2 May 2020
SeaBioComp is a collaborative project which is developing novel bio-based thermoplastic composite materials to replace conventional oil-based products in the industry.
The long term gain for the marine environment is very much at the forefront of this project as well as the development of viable new bio-composite materials, 3D printing of bio-composite materials and the development of analytical protocols to evaluate the long-term durability and reduced ecological impact on the marine environment.
For more information please visit:
http://seabiocomp.eu
and to be kept up to date with details of events, activities, deliverables etc please join the SeaBioComp Interest Group at http://www.seabiocomp.eu/interest_group/
Posted 2020-04-30 11:01:57
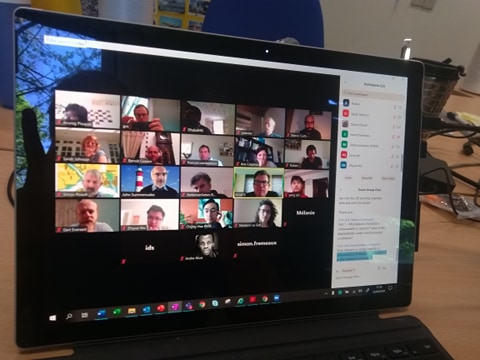
SeaBioComp General Assembly held online in April 2020
Due to the Covid-19 situation the SeaBioComp General Assembly meeting was held online at the end of April 2020.
Over 30 delegates joined the Zoom meeting at which all the Work Package Leaders presented updates of their work, precis of their activities and findings and answered questions from the partners listening in.
The meeting was successful in updating everyone on the excellent level of activities of the different areas of the project as well as future priorities. There was discussion regarding the delays in some areas of research and testing due to the worldwide lockdown but also some innovative and constructive thoughts as to how to work through the current restrictions.
Full details of the various Work Package updates are featured in the articles below.
Posted 2020-04-30 11:02:54
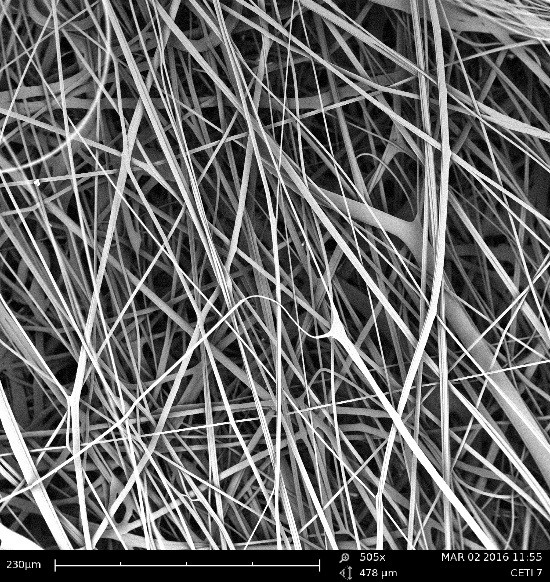
Natural Fibre Research and Selection for the project completed
Partners CETI and Centexbel have been investigating and evaluating the many natural fibres that can be used for manufacturing natural fibre composites.
The interest in natural fibres composites is growing rapidly due to their potential to replace synthetic fibre composites at lower cost and lower environmental impact. In addition natural fibres are a renewable resource for which production requires generally less energy compared to synthetic fibres. Many natural fibres can be used for the manufacturing of natural fibre composites and these were tested and evaluated as part of the SeaBioComp project.
The choice of the natural fibre in the composite is very important because the fibre used for reinforcement will directly affect the properties of the composite including elongation, strength and Young’s modulus. The main disadvantages of using natural fibres in the reinforcement of composites is the low thermal stability during fabrication and poor compatibility between fibre and matrix.
The SeaBioComp project has undertaken important research in order to give an overview of the different natural fibres available and of the different treatments which can be used to improve the interphase between fibres and matrix.
As a result of this work, two natural fibres have been selected (according to their environmental impact, cost, properties and availability) which will be used in the SeaBioComp project to manufacture pilot products. Flax and hemp were selected as the most suitable fibres to be used, due to a combination of their availability in Europe, mechanical properties, price and environmental impacts.
In the research, it was demonstrated that the level of retting is important and should be discussed with the supplier during purchasing. A high degree of retting enables easier splitting of the fibre bundles during fibre / matrix extrusion and injection moulding. This involves an increase of the mechanical properties with the degree of retting for both Young’s modulus and strength at breaking point.
The project research shows that it is necessary to improve the interface between fibre and matrix. Reinforcing fibres can be modified by physical, chemical or biological methods. Chemical treatments (such as alkali) are the most commonly used. Biological treatment (using enzymes) is becoming increasingly popular and offers particular benefit relating to environmental friendliness.
By making natural composite products using plant-based natural fibres as a reinforcement and biodegradable polymers as matrices, the project hopes that the ecological impact will be more than half compared to oil-based composites in addition to a 30 per cent reduction of CO2 emissions from their production.
Posted 2020-05-01 13:37:02
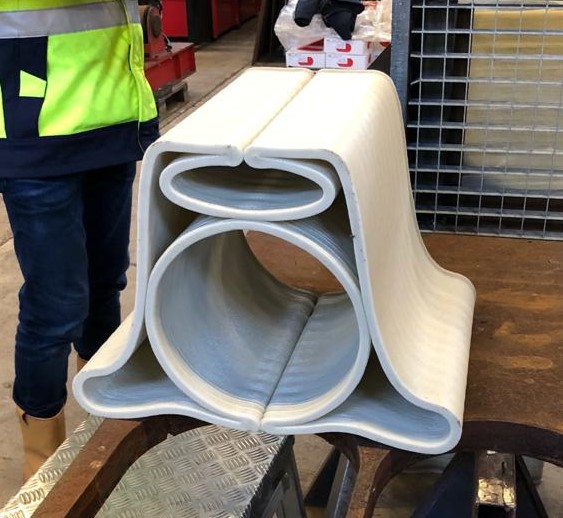
3D Printer produces first bio-polymer concept product for the marine sector
SeaBioComp has produced its first 3D printed biopolymer fender profile for use in the marine environment.
The fender profile was printed on an FDM Printer by Poly Products, a Netherlands based composite production and specialist engineering business, and partner in the SeaBioComp project, in collaboration with de Klerk Waterbouw who specialise in the installation of products for the marine environment.
SeaBioComp funded the research into the adaptations required to enable the 3D printing machine to process biopolymers which was undertaken by Poly Products. Research and testing into temperature control, natural fibre selection and corrosion of extruder parts were all thoroughly reviewed.
Project observer partner, De Klerk Waterbouw wanted to investigate the design and production of a bio-composite vertical fender profile for the berthing and guiding of ships, in order to replace traditionally used tropical hard woods and synthetic plastics. Collaboration with industry, end users, research establishments and public authorities is a key part of the SeaBioComp project, so a number of partners worked on the design, material selection, 3D printing, testing and evaluation of a scaled version of the biopolymer fender profile.
The findings from the material testing led by the University of Portsmouth and mechanical testing by De Klerk Waterbouw show very promising results and further optimization of designs, materials and production may lead to future full-scale production.
Commenting on the success of the 3D printing, Dr Albert ten Busschen, Poly Products, said: 'Using our 3D-printing technique, products can be made directly without the need of a mould. This saves the use of material and time. Moreover, there is no material spillage when a product is produced because no trimming or machining is necessary. Within the SeaBioComp project it is important that biopolymers can be printed with our 3D-printer. We printed the biobased polymers Thermoplastic Starch (TPS) and Poly Lactic Acid (PLA) on our machine to prove that we can make sustainable products for marine applications. Together with De Klerk we are now pursuing the development of full-scale fender profiles printed with biopolymers. We have completed mechanical tests and are now planning to print and install a full-scale printed fender profile with De Klerk to see how it works in practise.'
Ivo van Dalen, technical project leader of De Klerk Waterbouw is very enthusiastic: 'De Klerk Waterbouw has installed hydraulic engineering structures for over 150 years. We make large structures in docks and harbours from traditional materials like steel and tropical hardwood. But we are always open to new innovations and feel the responsibility to support a sustainable society. The SeaBioComp project opens possibilities for our company to make developments in that direction. The cooperation with Poly Products is very productive: we have jointly developed new, efficient and biobased fender profiles for berthing structures. With the production of full-scale prototype profiles we will undertake practical tests on the quay at our premises. Both our companies are oriented to develop solutions that are practical and efficient.'
The reports into the adaptations required for 3D printing of biocomposites and details of the 3D printed fender are available as downloads from the website. http://www.seabiocomp.eu/downloads/
Posted 2020-04-30 11:03:36
Finding the right biocomposite materials
Pollution in the oceans by non-degraded (micro-) plastics is a very serious problem of which there is a no practical solution once the plastic parts are discarded in the sea.
The development of industrial products using biodegradable or recyclable materials will be a solution and is the basis for the SeaBioComp project.
A number of project partners have been working on different areas of research and testing of a number of materials including the enhancement of properties of flax/PLA composites. Already the toughness of flax/PLA composites has been increased by up to 50% through the use of self-reinforced PLA biocomponent filaments.
Project partner Centexbel has been using their expertise to develop sheath/core PLA bicomponent filaments as a precursor to bio-based self-reinforced polymer composites.
CETI has been concentrating on the development of bicomponent multifilaments and nonwovens : spunbond, meltblown and carded, using bicomponent structures such as “islands in sea”.
IMT Lille Douai (associated lab of ARMINES) has used its expertise to develop manufacturing processes of composite materials/structures.
The University of Plymouth, with a background in composites manufacturing by RIFT (Resin Infusion under Flexible Tooling) will be looking at the use of biobased monomers for the fabrication of flax-reinforced thermoplastic composites.
Over the next few months project partners in Work Package 1 will be developing new types of hybrid preform which can be manufactured at an acceptable cost, while keeping high mechanical properties. The current form of flax/PLA composites are based on prepreg type material which has a relatively high cost. Also, the partners will be looking to optimize the mechanical properties further.
Posted 2020-05-12 10:33:30
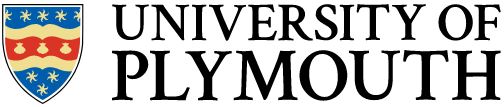
Choosing monomers to suit bio-composite production for marine applications
Choice of materials, resins and production techniques will significantly affect the cost, manufacturing process, mechanical properties and durability of the chosen composite materials.
The University of Plymouth, a partner in the SeaBioComp project have been reviewing current available thermoplastic monomers/resins suitable for in-situ polymerisation during monomer infusion under flexible tooling (MIFT).
In addition they have drawn up criteria for the selection of appropriate monomers based on processing temperatures and viscosity, mechanical properties, recyclability etc.
Full details of their findings and proposed choice of resin/monomer for the composite production in the project have been submitted to the academic publication Composites Part A: Applied Science and Manufacturing and is currently awaiting review.
Project Partners Ifremer, Armines and Centexbel also contributed to this report.
Posted 2020-04-30 11:46:47
Partners collaborate on testing of biocomposite materials
Project partners Ifremer, the University of Portsmouth and VLIZ have been conducting thorough and broad ranging testing of biocomposite materials in the quest to find suitable materials for pilot products for marine applications.
The University of Portsmouth has carried out extensive mechanical testing to understand flexural, tensile and drop weight limits.
Ifremer, the French Ocean Research Institute, have been conducting accelerated seawater ageing tests at different temperatures to study mechanical property changes. In addition they have been studying self reinforced PLA in terms of mechanical properties, seawater gain revealing promising long-term performance stability in marine conditions.
The Flanders Marine Institute VLIZ have been concentrating on micro-plastic formation and the ecotoxicity of the biocomposite materials. One clear result from the testing to date has been the need 3D print with smooth edges.
Future research will look at 3D printing filament to assess the quality of bio-based 3D printing materials as well as comparing fibres and filament qualities.
Posted 2020-05-12 15:14:19
VLIZ presents SeaBioComp poster virtually at SETAC 2020
Project partner VLIZ joined voer 1600 delegates online for the 2020 SETAC Annual Meeting to present a poster relating to the SeaBioComp project.
SETAC 2020 was a 5 day virtual event that featured training, networking and learning opportunities in the Science for Enhanced Global Environmental Protection sectors.
The VLIZ poster presented the work being done on the assessment of the degradability and toxicity of biobased composites as part of the SeaBioComp project. Details of the objectives of the research, the methodology and some preliminary results are all presented in the poster.
The poster attracted good social media activity and is available to download from the following link:
http://www.seabiocomp.eu/downloads/
Posted 2020-05-29 13:39:11
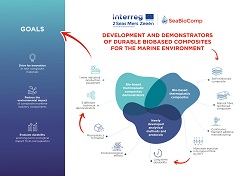
SeaBioComp leaflet and infographic
Organisations wishing to find out more about the SeaBioComp project are able to download the project leaflet and infographic from the website.
Anyone wishing to use any of these items at workshops, events or to send to colleagues and contacts are free to do so. Please attribute the publications to the SeaBioComp project.
To download the project leaflet, infographic or logo please follow the link:
http://www.seabiocomp.eu/downloads/
Posted 2020-04-30 11:04:07
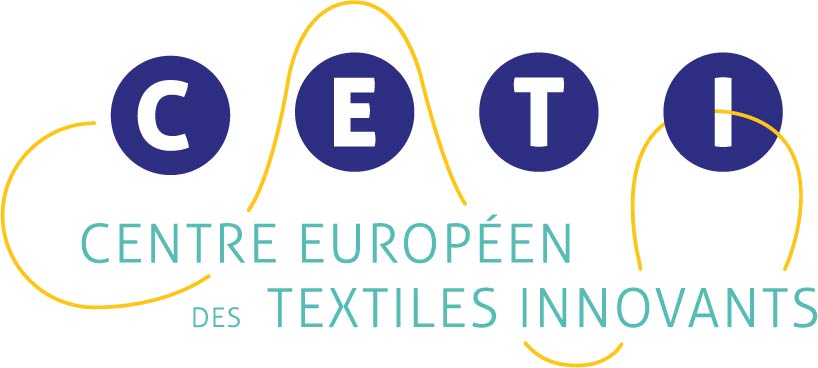
Focus on Project Partner CETI
The European Centre for Innovative Textiles (CETI) is a research and prototyping centre dedicated to innovation in textile materials, with prototyping and demonstrator realisation at its core.
The state-of-the-art weaving, braiding, knitting and finishing equipment is especially adapted to the research and development of composite materials.
In particular CETI is equipped with pilot spunlaid and drylaid nonwoven lines. These lines will be used in the SeaBioCOmp
project to develop non-wovens based on the project fibres.
Located at the heart of a first-class scientific network, the CETI uses creativity techniques that accelerate the innovation process from uses to solutions.
CETI brings together state-of-the-art equipment in one place to allow manufacturers to quickly advance from research to prototypes and small-scale production as quickly as possible.
For more information please visit:
https://www.innovationintextiles.com
Posted 2020-04-30 11:04:26
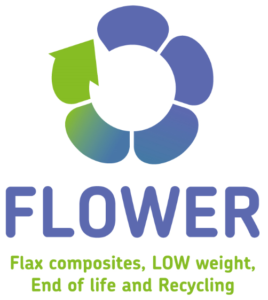
New findings from FLOWER Interreg project developing flax fibres reinforcements
The FLOWER Interreg project is aiming to develop flax fibre reinforcements for the composite industry at lower costs.
The project is hoping to use sustainable, cost effective and environmentally friendly lightweight composites as a viable alternative for automotive, advertising and sailing sectors which makes it of interest to the SeaBioComp project.
The project has recently published a paper on the 'Monitoring of mechanical performances of flax non-woven biocomposites during a home compost degradation'. The paper is available to view at the following link:
https://www.sciencedirect.com/science/article/pii/S0141391020300987?via%3Dihub
The University of Portsmouth is one of the partners in both the FLOWER project and SeaBioComp.
Led by the University of South Brittany, FLOWER brings together 4 academic partners (University of South Brittany in Lorient, INRA in Nantes, University of Cambridge and University of Portsmouth) and 4 industrial partners (the companies Kaďros, Teillage Vandecandelačre, EcoTechnilin and Howa-Tramico) located on both sides of the English Channel.
For more information please visit http://flower-project.eu/?lang=en
Posted 2020-05-11 18:25:12
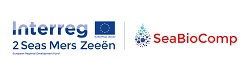
SeaBioComp is co-funded under the EU Interreg 2 Seas Programme
The project will run to August 2022 with an overall budget of Euro4.1M, Euro2.5M of which (60%) is funded from the European Regional Development Fund.
The SeaBioComp project partners include research institutions, university research groups, SMEs and specialist cluster organisations.
http://www.seabiocomp.eu